Budowa maszyn pneumatycznych opiera się na kilku kluczowych elementach, które współdziałają ze sobą, aby zapewnić efektywne działanie systemów wykorzystujących sprężone powietrze. Podstawowym komponentem jest sprężarka, która odpowiada za wytwarzanie sprężonego powietrza. Sprężarki mogą mieć różne konstrukcje, w tym tłokowe, śrubowe czy wirnikowe, a ich wybór zależy od specyficznych wymagań aplikacji. Kolejnym istotnym elementem są zbiorniki ciśnieniowe, które magazynują sprężone powietrze i stabilizują jego ciśnienie w systemie. W układzie pneumatycznym niezbędne są również zawory, które kontrolują przepływ powietrza oraz kierunek jego ruchu. Warto również zwrócić uwagę na siłowniki pneumatyczne, które przekształcają energię sprężonego powietrza w ruch mechaniczny. Oprócz wymienionych elementów, istotne są także przewody i złącza, które łączą poszczególne komponenty systemu.
Jakie są zastosowania maszyn pneumatycznych w przemyśle
Maszyny pneumatyczne znajdują szerokie zastosowanie w różnych branżach przemysłowych ze względu na swoją wszechstronność i efektywność. W przemyśle produkcyjnym wykorzystywane są do automatyzacji procesów, takich jak montaż, pakowanie czy transport materiałów. Dzięki swojej szybkości i precyzji, maszyny te przyczyniają się do zwiększenia wydajności linii produkcyjnych. W branży motoryzacyjnej maszyny pneumatyczne stosowane są do malowania pojazdów oraz do obsługi narzędzi pneumatycznych, co znacznie ułatwia pracę operatorów. W sektorze budowlanym urządzenia te są używane do podnoszenia ciężkich materiałów oraz do wykonywania różnorodnych prac wykończeniowych. Ponadto maszyny pneumatyczne znajdują zastosowanie w logistyce, gdzie służą do sortowania i pakowania produktów.
Jakie są zalety i wady maszyn pneumatycznych
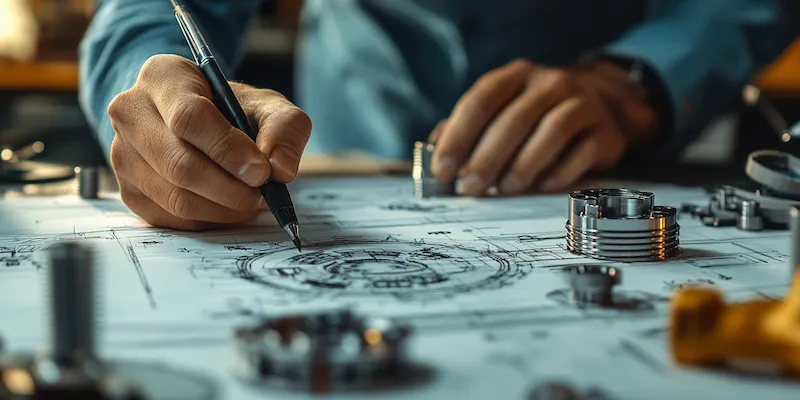
Maszyny pneumatyczne mają wiele zalet, które przyciągają uwagę inżynierów i menedżerów produkcji. Jedną z głównych korzyści jest ich prostota konstrukcji oraz łatwość w eksploatacji. Dzięki zastosowaniu sprężonego powietrza jako medium roboczego, maszyny te są zazwyczaj lżejsze i bardziej kompaktowe niż ich elektryczne odpowiedniki. Ponadto systemy pneumatyczne charakteryzują się dużą niezawodnością oraz niskimi kosztami utrzymania. Jednakże istnieją również pewne wady związane z ich użytkowaniem. Przede wszystkim wydajność energetyczna maszyn pneumatycznych może być niższa niż w przypadku systemów elektrycznych, co prowadzi do większego zużycia energii. Dodatkowo sprężone powietrze może być podatne na straty ciśnienia w przypadku niewłaściwego zaprojektowania układu przewodów. Warto również zauważyć, że niektóre aplikacje wymagają precyzyjnego sterowania ruchem, co może być trudniejsze do osiągnięcia w systemach pneumatycznych niż w elektrycznych.
Jakie są nowoczesne trendy w budowie maszyn pneumatycznych
W ostatnich latach obserwuje się dynamiczny rozwój technologii związanych z budową maszyn pneumatycznych, co wpływa na ich funkcjonalność oraz efektywność działania. Jednym z najważniejszych trendów jest integracja systemów pneumatycznych z nowoczesnymi rozwiązaniami automatyki przemysłowej. Dzięki temu możliwe jest zdalne monitorowanie i zarządzanie procesami produkcyjnymi, co zwiększa elastyczność i wydajność linii produkcyjnych. Kolejnym istotnym kierunkiem rozwoju jest miniaturyzacja komponentów pneumatycznych, co pozwala na tworzenie bardziej kompaktowych i oszczędnych rozwiązań. Wprowadzenie inteligentnych czujników oraz systemów sterowania umożliwia precyzyjne dostosowywanie parametrów pracy maszyn do aktualnych potrzeb produkcyjnych. Również ekologia staje się coraz ważniejszym aspektem projektowania maszyn pneumatycznych; producenci starają się ograniczać zużycie energii oraz minimalizować emisję hałasu związane z ich działaniem.
Jakie są kluczowe różnice między maszynami pneumatycznymi a hydraulicznymi
Wybór między maszynami pneumatycznymi a hydraulicznymi często zależy od specyfiki zastosowania oraz wymagań dotyczących wydajności i precyzji. Maszyny pneumatyczne wykorzystują sprężone powietrze jako medium robocze, co sprawia, że są lżejsze i bardziej mobilne. Z drugiej strony, maszyny hydrauliczne korzystają z cieczy pod ciśnieniem, co pozwala na osiągnięcie znacznie większej siły przy mniejszych rozmiarach. W przypadku aplikacji wymagających dużych obciążeń, hydraulika często okazuje się bardziej efektywna, jednak wiąże się to z wyższymi kosztami eksploatacyjnymi oraz większym ryzykiem wycieków cieczy. Kolejną różnicą jest szybkość działania; maszyny pneumatyczne zazwyczaj działają szybciej niż hydrauliczne, co czyni je idealnym rozwiązaniem w procesach wymagających dynamicznych ruchów. Warto również zwrócić uwagę na kwestie związane z konserwacją; systemy pneumatyczne są zazwyczaj prostsze w utrzymaniu, podczas gdy hydraulika wymaga regularnych przeglądów ze względu na ryzyko awarii spowodowanych uszkodzeniem węży czy złączy.
Jakie są najczęstsze problemy związane z maszynami pneumatycznymi
Maszyny pneumatyczne, mimo swojej niezawodności, mogą napotykać różnorodne problemy, które wpływają na ich efektywność i wydajność. Jednym z najczęstszych problemów jest spadek ciśnienia w układzie, który może być spowodowany nieszczelnościami w przewodach lub połączeniach. Nieszczelności te prowadzą do strat energii oraz obniżenia wydajności całego systemu. Innym istotnym problemem jest kondensacja wody w układzie pneumatycznym, która może powodować korozję komponentów oraz obniżać jakość sprężonego powietrza. Regularne osuszanie powietrza oraz stosowanie filtrów mogą pomóc w minimalizacji tego ryzyka. Ponadto operatorzy często borykają się z problemem niewłaściwego ustawienia zaworów, co może prowadzić do nieprawidłowego działania maszyn. Warto również zwrócić uwagę na zużycie elementów roboczych, takich jak uszczelki czy tłoki, które mogą wymagać regularnej wymiany.
Jakie są nowoczesne technologie w budowie maszyn pneumatycznych
W ostatnich latach technologia budowy maszyn pneumatycznych uległa znacznemu rozwojowi dzięki innowacjom w zakresie materiałów oraz automatyki. Nowoczesne materiały kompozytowe i lekkie stopy metali umożliwiają produkcję bardziej wytrzymałych i jednocześnie lżejszych komponentów, co przekłada się na ogólną efektywność systemu. Wprowadzenie inteligentnych czujników do monitorowania parametrów pracy maszyn pozwala na bieżąco śledzenie ich stanu technicznego oraz optymalizację procesów produkcyjnych. Dzięki zastosowaniu technologii Internetu Rzeczy (IoT), maszyny pneumatyczne mogą być zdalnie zarządzane i monitorowane, co zwiększa ich elastyczność i umożliwia szybsze reagowanie na zmieniające się warunki produkcyjne. Również rozwój oprogramowania do symulacji i analizy danych pozwala inżynierom na lepsze projektowanie systemów pneumatycznych oraz przewidywanie potencjalnych awarii przed ich wystąpieniem.
Jakie są perspektywy rozwoju branży maszyn pneumatycznych
Branża maszyn pneumatycznych stoi przed wieloma wyzwaniami i możliwościami rozwoju w nadchodzących latach. W miarę jak przemysł 4.0 zyskuje na znaczeniu, rośnie zapotrzebowanie na inteligentne rozwiązania automatyzacyjne, które integrują maszyny pneumatyczne z systemami zarządzania produkcją. Wzrost znaczenia efektywności energetycznej oraz zrównoważonego rozwoju skłania producentów do poszukiwania innowacyjnych rozwiązań, które zmniejszą zużycie energii oraz emisję gazów cieplarnianych związanych z działaniem tych urządzeń. Dodatkowo rozwijające się technologie cyfrowe umożliwiają lepszą analizę danych dotyczących wydajności maszyn, co pozwala na optymalizację procesów produkcyjnych oraz zwiększenie ich elastyczności. W przyszłości możemy również spodziewać się większej automatyzacji procesów konserwacyjnych dzięki zastosowaniu robotyki i sztucznej inteligencji, co przyczyni się do dalszego zwiększenia niezawodności systemów pneumatycznych.
Jakie są kluczowe aspekty bezpieczeństwa przy pracy z maszynami pneumatycznymi
Bezpieczeństwo pracy z maszynami pneumatycznymi jest niezwykle istotnym zagadnieniem zarówno dla operatorów, jak i dla całego zakładu produkcyjnego. Kluczowym aspektem jest zapewnienie odpowiedniego szkolenia dla pracowników obsługujących te urządzenia; znajomość zasad działania systemu oraz procedur awaryjnych może znacząco zmniejszyć ryzyko wypadków. Ważne jest również regularne przeprowadzanie przeglądów technicznych i konserwacji maszyn, aby upewnić się, że wszystkie komponenty działają prawidłowo i nie ma żadnych nieszczelności czy uszkodzeń. Dodatkowo stosowanie odpowiednich zabezpieczeń mechanicznych, takich jak osłony czy blokady bezpieczeństwa, może pomóc w ochronie pracowników przed przypadkowymi urazami podczas pracy z urządzeniami pneumatycznymi. Należy także pamiętać o właściwej organizacji miejsca pracy; upewnienie się, że przewody są odpowiednio zabezpieczone i nie stanowią zagrożenia potknięcia lub uszkodzenia może przyczynić się do zwiększenia bezpieczeństwa operacji.
Jakie są kluczowe czynniki wpływające na efektywność maszyn pneumatycznych
Efektywność maszyn pneumatycznych zależy od wielu czynników, które mogą znacząco wpłynąć na ich wydajność i niezawodność. Jednym z najważniejszych aspektów jest jakość sprężonego powietrza; zanieczyszczenia, wilgoć czy nieprawidłowe ciśnienie mogą prowadzić do obniżenia efektywności działania urządzeń. Odpowiednia filtracja i osuszanie powietrza są kluczowe dla utrzymania optymalnych warunków pracy. Kolejnym czynnikiem jest właściwe dobranie komponentów systemu, takich jak zawory, siłowniki czy przewody, które powinny być zgodne z wymaganiami aplikacji. Niezwykle istotna jest także regularna konserwacja oraz przeglądy techniczne, które pozwalają na wczesne wykrywanie potencjalnych problemów.